- 令和4年度 中小企業・団体編
- テックマイスター(埼玉県)
生産管理の改善を図れる人材育成のために
原価の仕組みと現場改善の方法を習得する
関口産業株式会社
- 事業内容
-
- 冷間鍛造及び精密機械加工
- 従業員数
- 75名
梅影 一男(うめかげ かずお)さん
令和2年(2020年)テックマイスター認定
平成27年(2015年)ものづくりマイスター認定(機械加工職種)
45年間大手時計メーカーの工作機械の開発課に勤務。主に部品加工の金型や治工具製造のため、汎用工作機械からNC工作機械加工に従事。生産技術の合理化や高精度マシニングセンタの開発から社内教育制度を作るなど人材育成教育や設備や装置の改善を行い、4件の特許取得や改善活動の推進、改善のためのシステム構築と合理化を図るなど、職場の生産性向上に貢献。
機械加工職種、特にNC工作機械・マシニングセンタ、数値制御フライス盤の実技指導や技能検定課題を用いた技能育成、プログラムの作成指導、作業標準化の手法教育と多能工育成、IE(Industrial Engineering)手法を使ったムダ取り改善、社内改善制度の提案と実施などを主に指導。
実施したプログラムの内容
実施プログラム
- 実施内容
- 原価の仕組み、利益を生み出す6S※の着眼点、6S運動の進め方、分析結果に基づく改善方法 6Sとは、「整理・整頓・清掃・清潔・しつけ」の5Sに加え「安全(Safety)」を加えた製造現場での職場環境改善のための活動のこと。
- 目 的
- 生産管理の改善を図れる人材育成のため
- 受講者
- 4名
- 実施日程
- 令和4年1月~3月 1回あたりの実技指導は3時間
- 1回目
- 利益を生み出す6Sの着眼点
- 2回目
- 6S運動の進め方
- 3回目
- 原価の仕組み、分析結果に基づく改善方法の指導
実技指導の目標と目標への到達度
No. | 目標 | 到達度 |
---|---|---|
01 | 職場の環境改善と社員のコストダウンに対する意識付けを目的とし、6S及び原価の仕組みについて理解する。 | 6Sに関する知識の習得及び6Sの効果について理解することができた。また、原価の仕組みとコストダウンについての知識を習得したと言える。 |
実技指導の成果
現場の作業環境について知識を習得したことで、少しずつではあるものの、整理・整頓ができるようになり、また社員にコストダウンの意識付けができた。
今後の課題
次年度も続けて実技指導を行う想定で、今回の3回のカリキュラムは原価管理やコストダウンの仕方までを座学中心でお教えしました。しかし、制度の変更で2年連続の実技指導が叶わなくなり、利益を出すまでの実践的な取組は残念ながら行えませんでした。
今後は若手社員への意識付けだけでなく、こうした実践編の取組を全社的に行うことで機会を捉えて技能習得してほしいです。
テックマイスターの
実技指導を依頼した理由
関口産業株式会社 代表取締役 堀井 重宏(ほりい しげひろ)さんに、
実技指導を依頼した背景や指導にあたっての準備などについて伺いました。
背 景
当社の主な事業内容は、冷間鍛造と精密機械加工による主に自動車、トラックの部品製造です。今回、テックマイスターの実技指導を依頼したきっかけとして、この数年で、電気自動車が徐々に増え、自動車本体の軽量化が必要になってきたことで、部品点数も相当数が減ると言われています。そのため、製造する製品を建設機械や医療用の部品などへシフトしていかなければいけないという危機感があります。
そのような状況もあり、工場内では、今年に入ってから、CAD/CAMを使うことで、今まで人が組んでいたプログラムの自動化や、冷間鍛造についても、昔は鍛造してみなければ分からなかった部分も解析ソフトを使ってシミュレーションするなどして生産性の向上を図ってきましたが、まだまだこれからというところもあります。
また、少しずつではありますが、生産性の部分で改善を行っていきたいと考えていたところでしたので年度の後半でしたが、埼玉県地域技能振興コーナーの担当の方と相談して、これまでものづくりマイスターとして指導いただいていた梅影マイスターに生産管理の改善などの指導も受けられると聞き、指導をお願いすることにしました。
指導は全3回、1回3時間で就業時間外に実施しました。社員4名はそれぞれ別の部署で、入社して数年目の20代です。受講する社員は梅影マイスターの実技指導を受けており、今回、自主的に参加を申し出た者たちです。
今までも社内教育として、研修などは行っていましたが、年に1~2日程度のものでした。その中で、埼玉県地域技能振興コーナーの方から紹介があり、ものづくりマイスター制度について知りました。こちらの要望に沿って、技能指導いただけるということで、今までにNC旋盤やマシニングセンタ、数値制御旋盤作業などを指導いただき、毎年3~4名の社員が技能検定に挑戦しています。
準備・環境づくり
指導内容は、梅影テックマイスターにご提示いただいた講習メニューの中から、当社に必要な内容を選び、マイスターが作成されたテキストなども拝見した上で、今回はこの3つをお願いしようということになりました。受講者は、梅影マイスターにものづくりマイスターとして指導いただいたことのあるメンバーで、お互いに現場の状況もよくわかっていることから引き続き同じメンバーにご指導いただくことにしました。
教材
講習のテキストは、梅影テックマイスターが作成された『6S基礎コース』と『生産現場のコストダウン基本事項』というオリジナルのテキストです。『6S基礎コース』は、51ページにわたり「6S」の定義や進め方など、基礎から演習までを穴埋め式で記入しながら学べます。もう一つの『生産現場のコストダウン基本事項』は、「コストダウン」とは何かということから、コストダウンの方法、原価の構成などが端的に説明されたテキストで、講義を聞きながらコストダウンの基礎が理解できるような内容です。
指導内容
テックマイスターの梅影 一男(うめかげ かずお)さんに、指導の詳細について伺いました。
ものづくりマイスターとして実技指導を行う中で入社して4~5年程度の若い受講者の方と仕事に対する姿勢などについて話をした際に、現場の生産性向上や原価の仕組みについて皆さんご存じないということがありました。特に中小企業さんだと、体系的な教育の機会がないということで関口産業さんの社員さんにしても、自分の仕事で手一杯で、現場の改善など他のことに目を向ける時間がなく、指導する方もいないため積極的には動けないということがよくわかりました。
関口産業株式会社さんへ以前ものづくりマイスターとして伺い、現場環境の改善の必要性を感じておりましたが、会社側でも同様に問題点と感じていたことから、今回6Sを中心に現場改善の考え方の基礎や、原価の仕組みから生産現場のコストダウンについて理解できるようにお教えしました。今回は全3回であったこともあり、座学を中心に行いました。
1回目は、「利益を生み出す6Sの着眼点」という内容で、『6S基礎コース』のテキストを中心に実技指導を行いました。関口産業さんへは何年も前から伺っており、工場内には「5S活動推進中」の看板が掲げられていますが、現場を拝見すると整理・整頓ができていなかったり、機械の前に踏み台を持ってきて危ない状態で作業する姿を目にしたりということがありました。また、工場内では毎週末、「5Sの日」を設けていますが、5Sに全員で取り組んでいるわけではなかったため、全社一丸になって工場で最も優先すべき「安全」を含めた6Sの取組が必要だと感じていました。そこで、今回の受講者4名に学んでいただくことにより、現場からの改善活動を進めてもらうことになりました。1回目では、テキストの項目「6Sとは」、「整理」、「整頓」、「清掃」、「清潔」、「しつけ」、「安全」、「確認テスト」の講義をしました。内容は「6Sの定義」、「6Sの特長」、「6Sの効果」、「6Sの展開方法」などです。また、整理・整頓の技術や具体案について、イラストや写真を用いて、実際の工場内における整頓対象箇所を説明しました。受講者には、理解できているかテキストの穴埋めによる確認や、整理・整頓の具体案を作成してもらいました。清掃・清潔・しつけはもちろんですが、特に「安全」については知識の定着を図りながら、自分たちの状況に照らし合わせて、作業の確実性を高め効率が上がるようテキストの演習を進めました。
2回目では、1回目の『6S基礎コース』に続いて、更に「6S」の内容を深めるため、PowerPointで作成した資料を用い『6S教育と活動』について、「6Sの定義」、「会社で掲げる6Sのスローガン」についての講義を実施しました。「6S教育と活動」では、企業の人財育成においては、「心・技・体の人づくり」が重要と考えており、6S教育は、特に「技(技能)」だけでなく、「体(企業体質改善の仕組みづくりなど)」や「心(モラルや向上心を持つことなど)」が重要であることを伝えました。予定どおり講義も進み、実務に直結する内容ということもあり、皆さん良く理解されていました。
3回目は、「原価の仕組み」についてです。毎日、同じような仕事をしていただけでは、自分たちの給料は上がっていかないということを説明しました。特に自動車関係は、毎年親会社からのコストダウンを要求されるので、経営者の方は大変な苦労をされています。堀井代表取締役とも相談し、本当は全社的な取り組みが必要なのですが、まずは若い方たちへの指導ということで、普段の業務内ではなかなか触れる機会のない原価の仕組みについて、お伝えしました。実際、給料というのは固定給があって、実会社で利益を上げていかないと給料も上がらないことを説明し理解していただけたと思います。内容は私が作成したテキストを用い、まず「原価」とは何かを伝え、「製造現場の原価構成」の表を見せながら何に費用がかかっているかを説明しました。その上で、「なぜ生産現場のコストダウンが必要か」、「コストダウンの方法」、「利益を出すためのコストダウンの具体的な方法」、「生産現場におけるコストダウン3つのターゲット」を伝えていきました。生産現場のコストダウンは、不良率の低減や改善などによるコストダウンです。原価の仕組みと、コストがどこにかかっているかを知ることで、生産管理がなぜ必要か、ムリ・ムダ・ムラをなくす改善活動がなぜ必要かがわかるようになり、現場全体の改善活動につながっていきます。
指導中は堀井代表取締役も毎回出席されて、組織として話を聞いていただく姿勢になっていました。今回は利益を出すまでの取り組みはできませんでした。また、2年目も続けてできればという希望はありましたが、令和4年度は続けての指導ができないということで、県の別の事業で幹部社員教育という形で、少し上の年齢の社員を対象に進めているところです。
また、現場の作業環境についても少しずつ整理・整頓ができるようになってきました。見ているとまだまだというところもあります。今後は、学んだことを他の社員にも展開していただき、取組をさらに進めていってほしいと思います。
テキスト抜粋
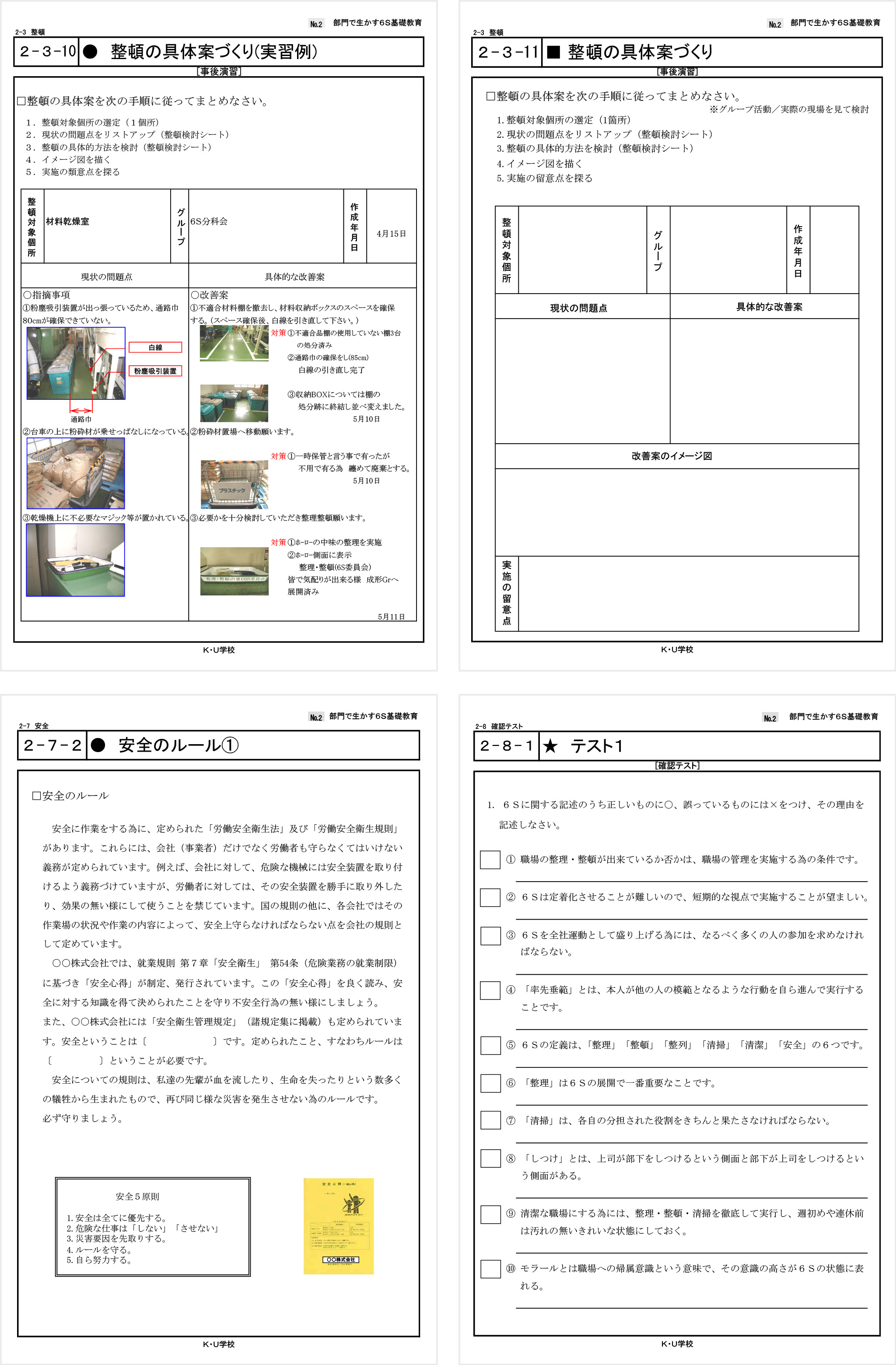
実技指導を終えて
受講者の関口産業株式会社 岡野 瞭(おかの りょう)さんに、実技指導を通して感じたことなどを伺いました。
NC旋盤のオペレーターをしています。梅影テックマイスターにはものづくりマイスターの実技指導でも教えていただいていたこともあり、テックマイスターの指導も受講しました。業務で課題と感じていたことは、会社から掲げられている目標や、改善目標が現場の方に出されているのですが、そこに対する意欲や積極性があまり高くなかったということがありました。また、仕事に対しては「これだけやっていれば」という気持ちと、「やはりこのままではいけない」という相反する気持ちがありました。
梅影テックマイスターに教わる機会をいただいたことで、意欲が高まり、仕事に対する姿勢も変わってきました。原価やコストダウンについては、自分の給料が固定給に入っていて、これは製品の中に含まれているということがよく理解できました。また、製品一つ一つに対する意識が変わり、これを作っていることで、自分の給料が出されているという意識が高まり、不良品などに対しての意識が変わってきました。
また、実技指導から半年経って、会社で設けられている清掃の時間にも、しっかり取り組もうという意識が芽生えてきました。また、6Sの中でも「安全」にも目を向けられるようになりました。安全第一の作業を意識することで、作業にムダがなくなり、作業の確実性が高まりました。一つ一つを丁寧に行うことで、結果、技能の向上にも繋がっています。
6S運動や、原価の仕組みを理解してコストダウンを図ろうとしても、1人では意味がないように思いますので、今後の目標としては、社員が一丸となって取り組み、それが会社全体に広がって、結果として個人に還元されるようにしていきたいです。以前に比べると、会社を段々と俯瞰して全体が見られるようになり、意識も変わってきたと実感できます。これからも継続して学んでいきたいと思います。
テックマイスターの梅影 一男さんに、指導して感じたことや受講者へ伝えたいことなどを伺いました。
受講されたのは若い方たちなので、リーダーを決めて主体的に動くような立場の方はおらず、おとなしい方だったかと思います。指導内容については、丁寧な説明を心がけましたが、項目によってはアウトプットするのに少し時間をかける必要がありました。また、毎回宿題を出しましたが、それにも皆さん時間をかけて取り組んでいたと聞いています。
彼らには知識として色々なことを学んで、身の回りのことから始めて、そこから他の人へも影響を与えられるように動いていってほしいと思っています。習得したことを展開するには、風通しの良い会社で、上下のコミュニケーションが取れることが重要です。受講者ではありませんが、今回は堀井代表取締役も一緒になってご協力いただけたので良かったと思います。今後は、幹部社員教育など全社的な取組が必要になってきます。ぜひ、会社全体で改善活動やコストダウンについての意識を高めていただきたいと思います。